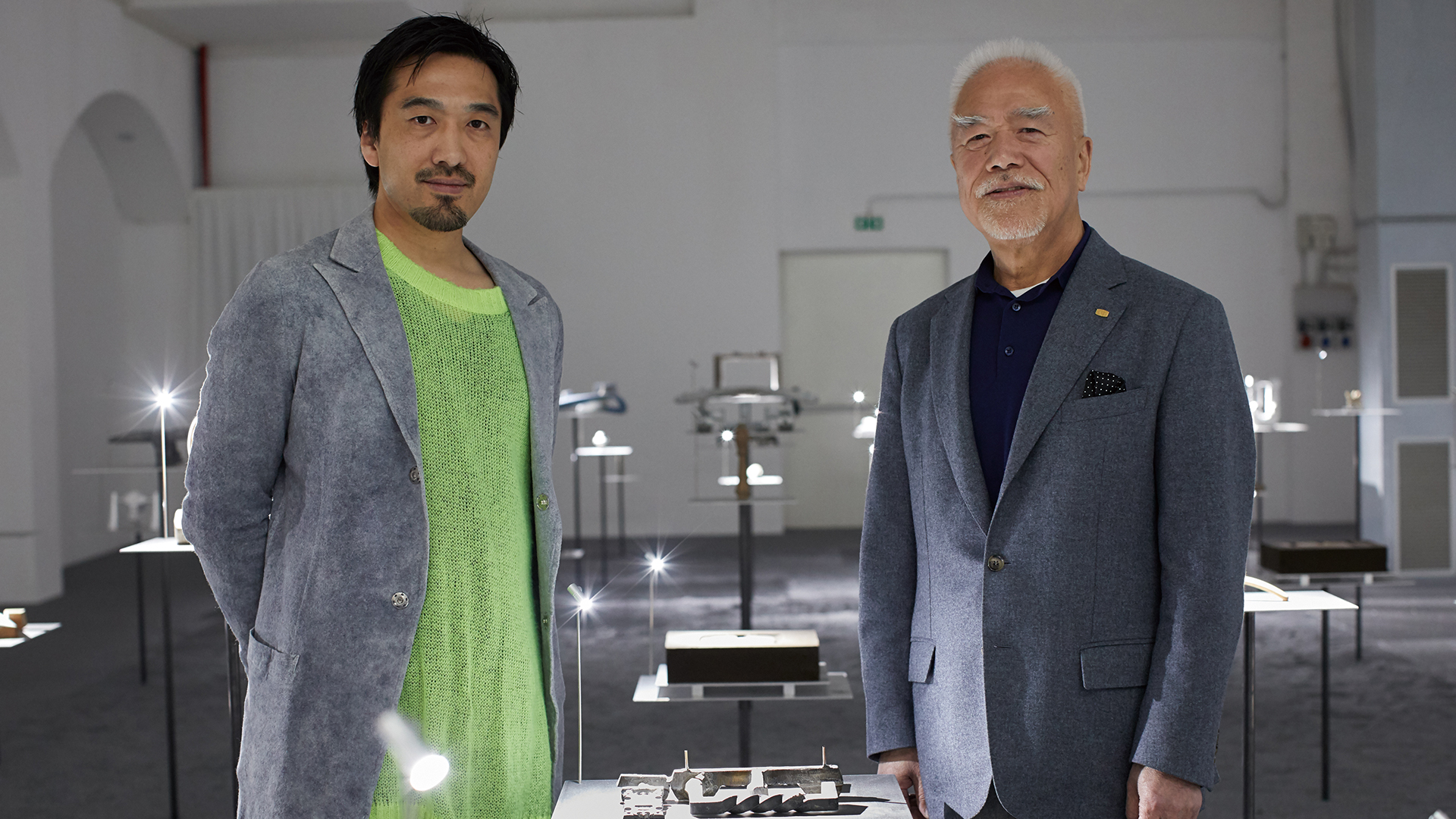
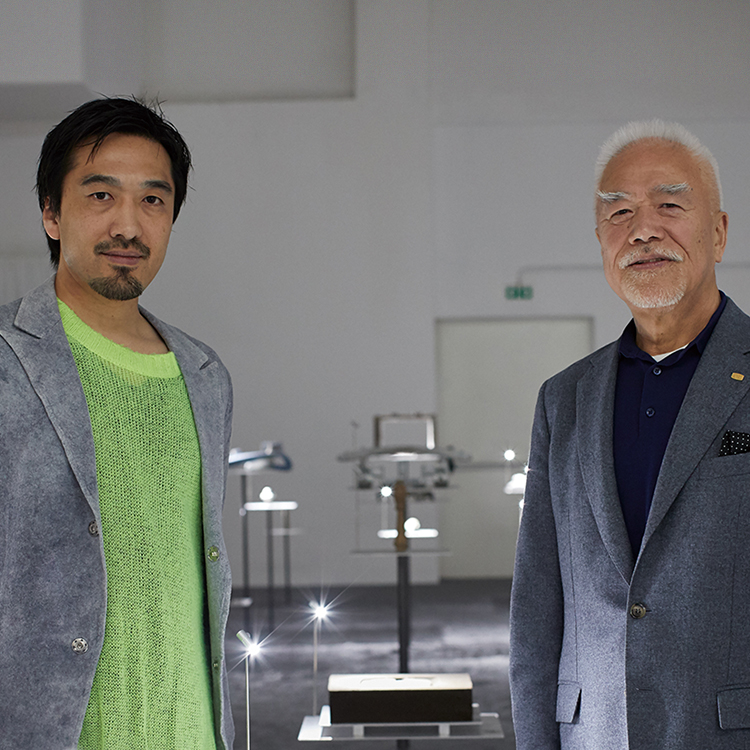
Junzo Tateno
CEO of UNION Corporation
Born in 1947, Junzo Tateno graduated from the Faculty of Law at Konan University (Kobe, Japan) in 1970
and entered Aoki Construction that same year. He joined UNION in 1973 and became CEO and President in 1990.
He serves as Chairman of the Union Foundation for Ergodesign Culture, a Public Interest Incorporated Foundation,
and the Osaka Industrial Bureau. He is also Vice Chairman of the Osaka Chamber of Commerce and Industry.
Tsuyoshi Tane
Paris-based Japanese architect
Tsuyoshi Tane is a Paris-based Japanese architect. He founded ATTA - Atelier Tsuyoshi Tane Architects in Paris in 2017 after being co-founder of DGT. Architects in 2006. Tsuyoshi believes in the idea of architecture belongs to a memory of place that connects its past to the future as his concept - "Archaeology of the Future." Tsuyoshi has received numerous awards, including Chevalier de l' ordre des Arts et des Lettres (FR, 2022) or the 67th Mainichi Design Awards 2021.
www.at-ta.fr
8
TATENO
Walking around the venue, I got the sense that everything had been laid out so visitors could easily pass by all the pieces on display. The first room had around 60 items for viewing. Had you decided on that number from the beginning?
TANE
Based on the concept One Design - One Handle, I selected 60 pieces for the first room in celebration of the 60th anniversary since UNION's founding. Towards the back of the exhibit, I wanted to recreate that feeling of surprise I had when first seeing where and how your handles are actually produced. At a time when metal molds and mass production are the norm, I thought using a traditonal sand cast to carefully craft each piece would create a nice juxtaposition between past and present.
■ 60 display stands glow against the darkness of the dimly-lit room. The floor is covered in a fine gravel that has been carefully painted silver.
TATENO
Illuminating each table individually really created a captivating atmosphere. If I'm not mistaken, you constructed this lighting system completely from scratch, didn't you?
TANE
I was trying to provide a close-up of the various tools, materials, and prototypes used in your work. Setting up the displays was the first time in my life to have such a face-to-face encounter with handles. I was transfixed by the materials and processes used to bring the designs to life. After carefully inspecting all the details of each handle -- these pieces in the greater architectural puzzle -- I began to see them as something like a sculpture in their own right.
TATENO
There are all types of handles; ones made from wood or glass or resin. But the origin of them all starts with the mold they are cast in. The sand-cast process shown at the venue is the exact one we were using at the time of our founding. UNION's history of handle craftsmanship began with the casting of aluminum. Through installations like this, we are again reminded that handles are the face of architecture.
■ Assorted materials, patterns, and tools used for casting are arranged neatly like works of art in a museum.
TANE
UNION is at the vanguard of manufacturers specializing in handles in Japan. You have worked with countless architects and designers over the years, but are there any projects that particularly stand out in your mind?
TATENO
That would have to be our project with Togo Murano. What was difficult about this project was that he asked us to encase a brass knurling rod (a metal bar covered in tiny indentations) inside an acrylic casing. The dimensions of the two materials are affected by temperature in idiosyncratic ways, so all of the handles we first produced ended up cracking to pieces. We were committed to meeting his request, however, so we kept trying and retrying various production methods until we started to see some new potential arise. Eventually, the skills of our craftsmen caught up to the task. Another time, I oversaw the installation of some handrails at a cafe (Printemps, now closed) designed by Murano in Shinsaibashi, Osaka. For this, we had to bring the handrails from the factory and shape them onsite, making minor adjustments along the way. That was an experience as well. We've faced a lot of tall orders over the years, but these have helped us develop the expertise, reliability, and undeniable craftsmanship UNION is recognized for in the architectural world today.
TATENO
For this installation, you focused on the tools and materials used to make handles as well as the origin of the mechanisms behind their craftsmanship. There's no denying that the number of people even within the industry who understand these basics is dramatically decreasing. In the past, sales staff used to go down to the factory or workshop and talk directly with the production manager or artisans. But this has changed with time. In pursuing expertise and more rationalized processes, I feel we may have segmentalized the various operations and roles in our business.
TANE
Well, the speed of communication and production capabilities have dramatically increased, haven't they? Today, the world demands streamlined processes where roles are assigned to each division and employees work in a systematic manner. There's not much room for face-to-face discussions
■ A wooden frame used at casting sites before the advent of metal frames is on display.
TATENO
After seeing this installation, I was again reminded of the need to re-educate and edify staff in the actual operations taking place at the production site.
TANE
We do need expertise in each field, but we also must have some interplay between professions to prevent siloing. The best relationships are the ones where each party has their own sense of responsibility and mission but can share in the joy of experiencing something everyone has made together. Without this mindset, you just can't build great architecture.
■ Sand gradually turns black from heat as the sand mold casting process is repeated.
TATENO
I get the impression that a lot of young people today don't work with much of a dream or vision for the future. Did you decide to base yourself overseas because you couldn't realize the dream you wanted for yourself here in Japan?
TANE
I'm nothing but big dreams. *Laughs* It kind of just happened naturally that I ended up overseas. When I was in my second year of university, I took a solo trip around Europe, and this had a big impact on me. The diversity of the people there, the distinct culture and history of each region manifested in the stunning architecture. It was all stuff I had never seen before. And I had only scratched the surface of what this place had to offer. This inspired me to start exploring more of our vast world and to keep pushing myself in the process.
TATENO
My father had an adventurous spirit as well. He couldn't speak a lick of English and hated planes, but one day in his 40s, he decided to spend one month traveling around the world. He told me that after seeing the latest architectural handles being used abroad, he was both confident and reassured in the exceptional quality of the work he was doing. I sometimes still look at the journal he took with him to record the details of that trip. He always told me to associate with the very best. By spending time with top architects and artisans and other distinguished figures, you learn to refine your sensibilities, leading you to create exceptional work in the end. How did you cultivate your sensibilities?
■ CEO Tateno speaks of his father's trailblazing spirit and the message he passed down.
TANE
First and foremost, I try to keep a strong sense of curiosity. I'm interested in the things that surround me in life and store the inspiration they provide deep inside me. This transforms at some point into the ability to create something new. I am always trying to challenge myself and testing the limits of what is possible. We live in an age overflowing with information and material things, but I make sure not to settle for the status quo and ask myself what it is I really want to do. If something's impossible, I think about why that's so. By taking that next step, I arrive somewhere new which brings me joy. I believe this gives me the chance to create a future people will be drawn to.
■ Tsuyoshi Tane reflects on his career and the many challenges he has undertaken.
TANE
An important objective for this installation was making sure it became something more than a personal challenge. It needed to provide momentum and inspiration to both UNION and the current generation. Bringing several tons of earth to Milan Design Week and demonstrating the process of molding objects from a sand cast was not the whole point. The very act of taking a challenge like this I believed would reveal a new future for handles. What is a handle? By exploring this primordial question through the lens of archaeological excavations and scientific research, I felt the answer would become clear, as would the path forward.
■ The space was designed to resemble a laboratory, concentrating attention on the sand-mold casting process.
TATENO
I will never forget when you told me "let's go back to the very beginning and create UNION's future." If I was in charge of the installation, I never would have come up with this. I would have said let's lay out a few thousand handles you've produced up until now and announce a few new designs and that would be it. The 60th anniversary of our founding marked the first time in 13 years since we exhibited at Milan Design Week. Rather than simply presenting the beauty of our hardware, I wanted to test just how much handles and the people and processes that make them could excite people's imaginations and lead to new realizations.
■ Visitors from around the world watch as Japanese artisans demonstrate casting techniques.
TANE
Why do we need handles? How did they come into being? What's the meaning behind a given design? While the technology for making handles has improved, we've stopped thinking about the fundamental reasons behind what we do. We've gotten caught up in process of thinking: if I'm a manufacturer, I must manufacture; or if I'm a designer, I must design. Often, we lose sight of what actually is created when all is said and done.
TATENO
Handles work through the hand to leave an impression on the mind. They have a big influence on our experience of a place or the impression a room creates.
■ Molten metal (in this case, tin) is poured into a hardened sand cast.
TANE
If we didn't have handles, we wouldn't be able to get into places to start. When you're inside a building you may not touch much of what's around you, but you do touch the door knobs, handles, and railings. The sensations you get from that contact affect your impression of the space you're in. The moment you grab that handle and open the door is like exchanging a handshake with the architecture before you. It's almost a sacred act. That's why manufacturers with a standard line of products reflecting their ideals enjoy such long-standing trust.
TATENO
Trends die quick, but inherent charm possessed by a superb finish or quality materials rarely changes. True craftsmanship withstands the test of time and is loved by every generation. When I was looking at this installation, I was reminded of this truth we must never forget. Structures like Gaudí's Sagrada Família or Hōryū-ji in Nara were painstakingly thought over and constructed, which has given them something that transcends geographical regions or periods in time to capture the hearts of all.
■ Sand is brushed off a handle just removed from its mold. After any remaining burrs or runners have been removed from the edges, the piece will be complete.
TANE
How long will it be used? How long do you want it to be used? Finishing the project is not the ultimate goal. The quality of architecture is dramatically affected by whether or not the people making its constituent parts envision them being used well into the future. The culture of craftsmanship which has broken free from the molds of conventional architecture will continue to create new value that is timeless and universal.
Photo : Sohei Oya
Writing : Hisahi Ikai